Tradicionalmente, os fatores de produção considerados essenciais ao processo produtivo são a terra (terras cultiváveis, florestas, minas, recursos naturais), o trabalho (o homem) e o capital (máquinas, equipamentos, instalações). A eficiência combinada desses três fatores tem se mostrado vital para as empresas sucroenergéticas.
Uma boa eficiência agrícola irá propiciar a matéria-prima na quantidade e qualidade requeridas pelo processo produtivo. Da mesma forma, a eficiência conjugada do trabalho com máquinas e equipamentos é que irá garantir o melhor aproveitamento do açúcar presente no caldo da cana e do poder calorífico do bagaço.
Além desses 3 fatores tradicionais, gostaria de incluir a tecnologia como um fator cada vez mais importante na busca da eficiência global. Analisando o processo decisório do ponto de vista top-down, a definição do que produzir, quanto produzir de açúcar, etanol hidratado, anidro, energia tem origem no planejamento que considera, para um determinado horizonte de tempo, a demanda, o preço de venda, o custo, a capacidade de cada usina e os riscos associados.
Uma vez definido o que a usina deve produzir, as decisões recaem sobre a melhor utilização dos fatores produtivos (trabalho, capital e tecnologia), considerando os aspectos de segurança, de restrições operacionais e de projeto. Todo o processo de produção industrial mundial vem passando por uma revolução, na qual é preciso ter controle total da produção para garantir qualidade, flexibilidade e produtividade no processo fabril.
E o mercado sucroenergético não é exceção a esse contexto, com os desafios adicionais de reagir às variabilidades climáticas e de mercado típicos desse setor. Esse desafio leva à necessidade de novos tipos de tecnologias dinâmicas, de aprendizagem e interativas. Essa necessidade do setor possui bastante similaridade com o objetivo da Indústria 4.0, que busca obter ganho na eficiência pela otimização de toda a cadeia de produção, via análise de dados complexos e informações trocadas entre sistemas físicos e digitais, a fim de permitir que sejam feitos ajustes produtivos em tempo real.
Para atingir esse objetivo, várias tecnologias passaram a compor o espectro de ferramentas associadas à Indústria 4.0:
• Simulação ou Gêmeos digitais: Na Indústria 4.0, a simulação computacional é utilizada em plantas industriais para análise de dados em tempo real, aproximando o mundo físico e virtual, e no aperfeiçoamento em configurações de máquinas para testar o próximo produto na linha de produção virtual, antes de qualquer mudança real, gerando otimização de recursos, melhor performance e mais economia.
• Integração de sistemas (por exemplo, integração de dados de processo e de qualidade que, geralmente, estão em redes distintas).
• Internet das Coisas (IoT). A internet das coisas (em inglês, IoT – Internet of Things) consiste na conexão entre rede de objetos físicos, ambientes, veículos e máquinas por meio de dispositivos eletrônicos embarcados, permitindo uma coleta e troca de informações mais rápida e efetiva. Na indústria de produtos e serviços, a IoT representa a integração de tecnologias que, antes, não estavam conectadas e que, agora, estão interligadas por meio de uma rede baseada em IP.
• Segurança cibernética.
• Computação em Nuvem.
• Realidade aumentada.
• Big Data e Analytics: Análise e gestão de grandes quantidades de dados propiciam o aumento de performance e a otimização dos processos industriais, equalizando o consumo de energia com a qualidade de produção, ao propiciar uma melhor leitura de cenários e tomadas de decisão mais velozes.
• Inteligência Artificial e Machine Learning (computador simulando a inteligência humana e/ou buscando soluções por “autoaprendizado”).
• Robótica e Automação.
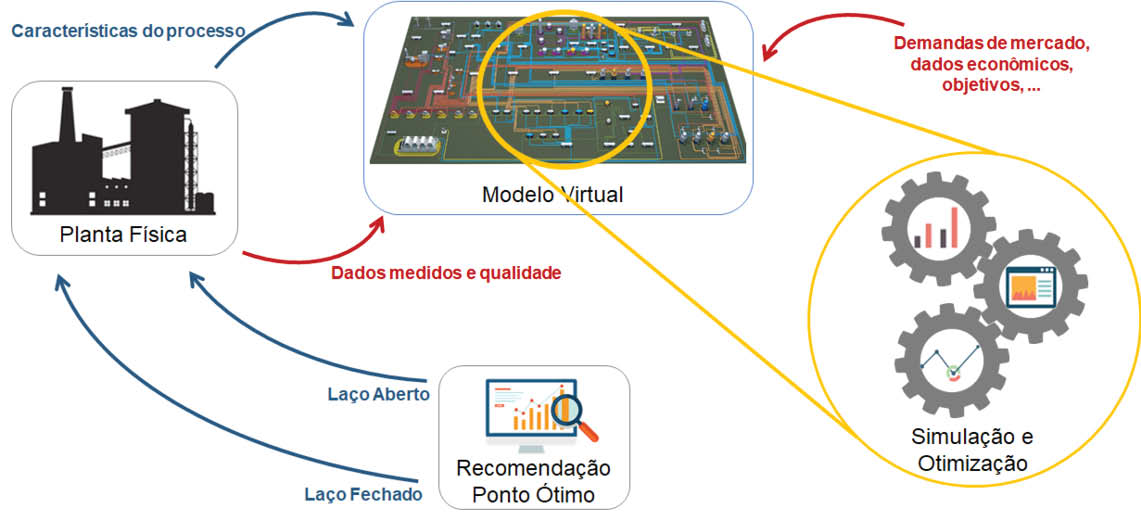
Uma técnica que tem recebido maior atenção na indústria de processos para otimizar o desempenho global da planta é o Real Time Otimization. O RTO procura otimizar o desempenho do processo (podendo ser medido em termos de lucro, custo operacional ou eficiência global), possibilitando que as empresas possam aumentar a sua rentabilidade nas diversas condições da planta, e, nele, estão embarcados muitos conceitos de Indústria 4.0.
O RTO baseia-se num modelo fundamentado nos princípios da engenharia para determinar um conjunto de valores de
setpoints, que maximizem o objetivo definido pelo estratégico. Mas, de posse de todas essas informações, fica sempre a pergunta de como transformar uma planta sucroenergética em uma Usina 4.0. Ao meu ver, os principais elementos de uma solução para a Usina 4.0 devem contemplar:
• Possibilidade de operação em tempo real (automatismo);
• Os dados são adquiridos e tratados quase instantaneamente, o que permite que decisões sejam tomadas rapidamente;
• Criação de “cópias virtuais/gêmeos digitais” das fábricas físicas (simulação e otimização em tempo real);
• Modelos representativos da planta real (via software, agregam-se informações de engenharia, restrições, dados dos sensores, dados de qualidade e seu inter-relacioamento-integração, IoT, inteligencia artificial);
• Otimização global (inteligência artificial);
• Escalabilidade;
• As decisões poderão ser tomadas a partir do mundo ciberfísico, de acordo com as necessidades da produção. Outro ponto é que as máquinas fornecerão informações relevantes sobre o resultado da atuação, possibilitando o ajuste e o refinamento da solução (Machine Learning).
Como passos a serem seguidos para passar de uma operação tradicional para uma Usina 4.0, cito:
1. Planejamento de uma estratégia realista para a entrada na Indústria 4.0: Se faz necessário avaliar a maturidade digital de seu negócio no atual momento, projetando onde você precisa estar, definindo metas claras para reduzir o gap, priorizando as medidas que trarão mais valor ao seu negócio e garantindo que elas estejam alinhadas com a estratégia geral.
2. Identificação de uma solução que atenda aos desafios do setor: Seguindo o mantra de uma das usinas mais inovadoras do setor: Pense grande, comece pequeno, mas começe o mais rápido possível. Pensar grande significa que se deve mirar uma solução que contemple todos os setores, mesmo que não seja implementado de início.
Isso para garantir que o objetivo da maximização global possa ser atendido dentro de uma mesma plataforma. Começar pequeno no sentido de um projeto com pouco investimento, mas com retorno atrativo, que gera confiança e credibilidade para voos maiores. Começar o mais rápido possível, para que não se espere uma condição ideal de infraestrutura para o seu início, pois as condições ideais nunca existirão, e estaremos abrindo mão dos ganhos e do conhecimento melhor da planta.
3. Planejamento dos investimentos tecnológicos que precisarão ser feitos: A intenção é que se possam direcionar os recursos da sua empresa para a aquisição de tecnologias realmente úteis, sem precisar, por exemplo, trocar todo o seu maquinário ou
realizar investimentos em medidores não necessários. A experiência indica que, atualmente, 90% das indústrias do setor possuem nível de instrumentação e automação suficientes; o importante é que as informações estejam acessíveis num ambiente de rede integrada.
4. Envolvimento de todos: Para o sucesso, é imprescindível que todos os envolvidos estejam comprometidos com a abordagem.
5. Treinamento, Capacitação e Adaptação às mudanças: Na Indústria 4.0, a tecnologia é utilizada para transformar dados em vantagem competitiva. No entanto, nem todos têm uma cultura digital, razão pela qual especial atenção deve ser dado para gerar um ambiente colaborativo entre o pessoal pouco afeito à tecnologia, mas com experiência operacional, e aquele afeito à tecnologia, mas com pouco conhecimento prático da operação. Agregando o recurso tecnologia aos fatores tradicionais, iremos atingir um novo patamar de operação e rentabilidade.