O setor sucroenergético é tradicionalmente reconhecido por desenvolver, em maior quantidade, soluções inovadoras caracterizadas como incrementais ou evolutivas utilizando tecnologia em diversas áreas. Um bom exemplo é o de planejamento e controles de processo, equipamentos, processos e insumos. Historicamente, foram iniciativas com foco principal em ganhos de eficiência e redução de custos.
Recentemente, sob uma ótica mais disruptiva, a agroindústria tem-se posicionado estrategicamente ao buscar novos processos, produtos e negócios. Refletindo sobre os assuntos relacionados a controle de processos, eu me lembrei de quando comecei a trabalhar no setor há quase 40 anos, no CTC (Centro de Tecnologia Copersucar), onde o controle de pH na dosagem das usinas era feito utilizando papel tornassol.
Ao longo desses anos, pude acompanhar uma evolução tecnológica incrível, desde os modelos pneumáticos analógicos, passando pelos digitais fieldbus e, recentemente, chegando às fibras óticas, Hart, Ethernet Industrial e protocolos IoT, apoiados por redes móveis de alta capacidade de conexões, confiabilidade e largura de banda, como o 5G e o Wireless Hart, que viabilizaram trocas de informações entre dispositivos eletrônicos, sensores, atuadores e controladores em tempo real dentro do ambiente industrial, com flexibilidade e segurança de maneira bastante intuitiva.
No meio desse processo de transformação digital, a conectividade permitiu que, já no início dos anos 2000, fossem feitas as implantações dos primeiros COI’s (Central de Operações Industriais), permitindo controlar as operações de toda a planta de forma centralizada e remota.
Nos últimos anos, tem acontecido uma rápida e ampla difusão de tecnologias digitais nas cinco plantas da São Martinho (quatro de cana e uma de milho), das quais já foram implantados: Gêmeos Digitais, que são simuladores de processo e que, de maneira offline, permitem estudar diversos cenários, projetar adequações/ampliações nas plantas e planejar a safra; já online é possível fazer a gestão da rotina dos processos acompanhar a gestão e o desempenho das plantas utilizando o PGDI (Planejamento da Produção e Gestão do Desempenho Industrial) e o GDI, além do dashboard com a árvore de indicadores que permite a visualização consolidada dos principais indicadores de performance,
permitindo a interação em tempo real da equipe técnica corporativa com as equipes da operação alocada nos COI’s de cada uma das unidades. O COI corporativo do Grupo São Martinho já está no segundo ano de atividade, e, com as tecnologias implantadas, já é possível perceber bons reflexos nos resultados das unidades: aderência ao planejado, incremento nos rendimentos e eficiências e ganhos de produtividade, qualidade e estabilidade dos processos.
Os processos têm aderido a novas tecnologias de sensoriamento que incluem, além de sensores tradicionais, os sensores de espectro de infravermelho próximo (NIRS), sensores especiais, sensores virtuais, visão computacional e nano sensores.
Ainda há o crescente uso das tecnologias de armazenamento, gerenciamento e uso de dados apoiados nos conceitos de Analytics e Big Data como essência para tomadas de decisão, suportadas por uma grande quantidade de dados, que são gerados em tempo real e historiados. Dados esses que são capazes de gerar informações suficientes para que as decisões sejam certeiras e inteligentes, permitindo a otimização em tempo real ou no menor tempo possível.
A manutenção preditiva e a chamada Inteligência Artificial têm gerado a auto-otimização de processos e parâmetros. Com esta visão, estamos implantando controles avançados e laços fechados nas diversas etapas do processo, com parcerias de alto nível técnico. De acordo com nosso plano estratégico de automação industrial, onde definimos os critérios de automação, autonomia e inteligência de processos, há a previsão de operacionalizar as plantas autônomas em até cinco anos. Sendo assim, tecnologias, processos e pessoas devem estar muito integrados durante todo o processo de transformação digital, para que as tecnologias e ferramentas gerem valor aos usuários e avancem com poucos retrabalhos.
Convivendo com todas estas transformações ao longo dos anos, ainda é muito comum no nosso setor algumas operações realizadas manualmente, que oferecem riscos de segurança e incomodam bastante, como por exemplo: limpeza de equipamentos de troca térmica, em especial evaporadores (hidrojato); chapisco de moenda; descarregamento de cana (operação de Hillos), entre outras.
O aparato tecnológico tem evoluído nesse sentido com o desenvolvimento de robôs para chapisco, arame e/ou vareta; limpeza de evaporação via química (já realidade na São Martinho) ou com utilização de robôs (em desenvolvimento); operação de Hillos através de visão computacional com análise de imagens, e tantas outras soluções. Estas são algumas das inciativas que nos permitirão habilitar o futuro da São Martinho e do setor, trazendo novos conceitos de operação e ajustando ao cenário futuro que vislumbra a integração harmônica entre mão de obra, cumprimento das rotinas e execução dos processos de manutenção.
O futuro das tecnologias industriais passará por inúmeras dimensões, para isso muitas inovações e ferramentas têm-se apoiado na construção desta visão de longo prazo, como por exemplo:
• Explorar o conceito de operação assistida com auxílio tecnológico – onde o operador recebe uma nota em função da sua operação durante seu turno, identificando oportunidades e direcionando possíveis ações de capacitação deste mesmo colaborador;
• Simuladores para treinamentos técnico-operacionais – onde o operador pode reciclar seu conhecimento, e novos operadores têm a oportunidade de aprender como operar em situações simuladas;
• Gerenciamento da rotina – tem sido uma prática fundamental para reduzir o distanciamento dos operadores com os equipamentos e procedimentos que se tornam cada vez mais automáticos no dia a dia da operação.
Aproveitando para falar um pouco sobre insumos industriais, que é o terceiro maior item na composição dos custos de produção, algumas evoluções recentes são muito promissoras e outras já são realidade nos aspectos de redução de custos e aumento de eficiência, podendo citar:
• Utilização de enzimas no processo de produção do açúcar, com foco na “quebra” da cadeia de polissacarídeos presentes, como amido e a dextrana, reduzindo a viscosidade dos caldos, massas e méis e contribuindo nas trocas térmicas, na decantação e principalmente nos cozimentos (levando a uma menor viscosidade e, como consequência, maior taxa de cristalização) e nas centrífugas (melhor purga dos méis), com resultado positivo no rendimento de fábrica;
• Enzima na fermentação com atuação nos precursores de formação de espuma, reduzindo significativamente o consumo de antiespumantes e dispersantes;
• Enzima com atuação em infermentescíveis, atuando na “quebra” em monômeros fermentescíveis, reduzindo os açúcares residuais com reflexo positivo no rendimento fermentativo;
• Fermento GMO – uma realidade já consolidada e em constante evolução no processo do milho, também faz parte da rotina do processo da cana, onde o desafio maior foi, em função do reciclo, a garantia da permanência da levedura no decorrer do tempo, reduzindo principalmente a formação de glicerol e trazendo ganhos no rendimento fermentativo;
• Estamos também acompanhando e fomentando testes/aplicações com bateriófagos, microrganismos que “predam” bactérias contaminates da fermentação alcoólica, focando na substituição de insumos de alto custo e aumentando a eficácia do controle de contaminação;
• Bacteriocinas – produtos inovadores obtidos a partir de bactérias que possuem ação antimicrobiana específica com os mesmos objetivos dos bacteriófagos.
Simultaneamente, existem muitos desenvolvimentos acontecendo, envolvendo muitas pessoas, pesquisas e empresas qualificadas. Para acompanhar toda esta evolução, estamos participando ativamente e acompanhando bem de perto os avanços do mercado.
Partindo para a linha de equipamentos e com a recente chegada da tecnologia de produção do milho aqui no Brasil, algumas soluções tecnológicas podem e estão sendo adaptadas/aplicadas para o mercado de cana, como alguns exemplos:
• Utilização de decanters e tricanters em processos de separação;
• Chiller para resfriamento de água para fermentação e destilação (o que não é uma novidade, mas reforça a importância dos conceitos de eficiência de processo);
• Projetos de destilação, desidratação e evaporação de vinhaça integrados. No nosso projeto de milho na Usina Boa Vista, essas três operações integradas consomem apenas 1,05Kg de vapor de escape por litro de etanol anidro;
• Utilização de compressores mecânicos para vapor de processo (substituindo consumo de vapor por consumo de energia elétrica) – levando à redução de consumo de vapor no processo e sobra de bagaço;
• No processo de produção do açúcar, estamos implantando na Usina São Martinho o resfriador de açúcar a placas, com água gelada como fluído de resfriamento, após os secadores existentes, garantindo controle adequado da temperatura do açúcar, com melhor controle da qualidade do açúcar na armazenagem;
• Na linha de geração de vapor, acabamos de colocar em operação, também na São Martinho, uma caldeira de 450t/h, 100Bar e 520oC, com leito fluidizado, ciclo regenerativo e precipitador eletrostático. Muita coisa está acontecendo.
Um outro importante projeto nosso foi a instalação da planta de produção de etanol de milho no conceito Flex Full, operando junto à planta de etanol de cana em Quirinópolis-GO, na Usina Boa Vista, produzindo etanol anidro, DDGS e óleo de milho. As plantas são energeticamente autossuficientes devido à integração energética, sem a necessidade de complemento de biomassa. Além disso o biometano já é realidade, a partir da vinhaça e da torta de filtro.
Linhas de desenvolvimento estão acontecendo no mundo e também no Brasil. O conceito de biorrefinarias está ganhando cada vez mais robustez, onde nosso segmento tem mantido uma posição estratégica, vantajosa e muito significativa para viabilizar a produção do SAF (Sustainable Aviation Fuel), partindo do etanol com menor pegada de carbono do mundo – por meio de tecnologias como:
AtJ (Alcohol-to-Jet); também SAF e/ou e-metanol a partir do CO2 biogênico disponível nas nossas fermentações - PTL (Power-to-Liquid); biopolímeros originados também a partir do etanol; hidrogênio verde (água e energia elétrica), entre “outras cores” – através da reforma do etanol e/ou biometano;
Da riqueza do nosso bagaço/palha disponíveis, além da produção de energia elétrica já muito difundida, também oportunidade para a produção do etanol de segunda geração (E2G), processo que temos exemplos de mercado ao redor do mundo todo, podendo ser também matéria-prima para produção de biometano (processo em desenvolvimento), produção de hidracarbonetos (gasolina verde, diesel, querosene...) a partir de gás de síntese (CO + H2) através de processos de decompasição térmica de biomassas - gaseificação.
É possível sonhar alto!
Temos muito trabalho pela frente, mas certamente este momento de transformação tecnológica vai levar nosso segmento para um outro patamar de protagonismo, não só no Brasil como no mundo.
E para finalizar, atualmente, uma série de tendências tem influenciado o agronegócio brasileiro, onde o setor sucroenergético, com a “riqueza” da cana, se insere perfeitamente nos conceitos de ESG, economia circular, descarbonização, além da transformação digital já explorada acima, todos intimamente relacionados com tecnologia e inovação.
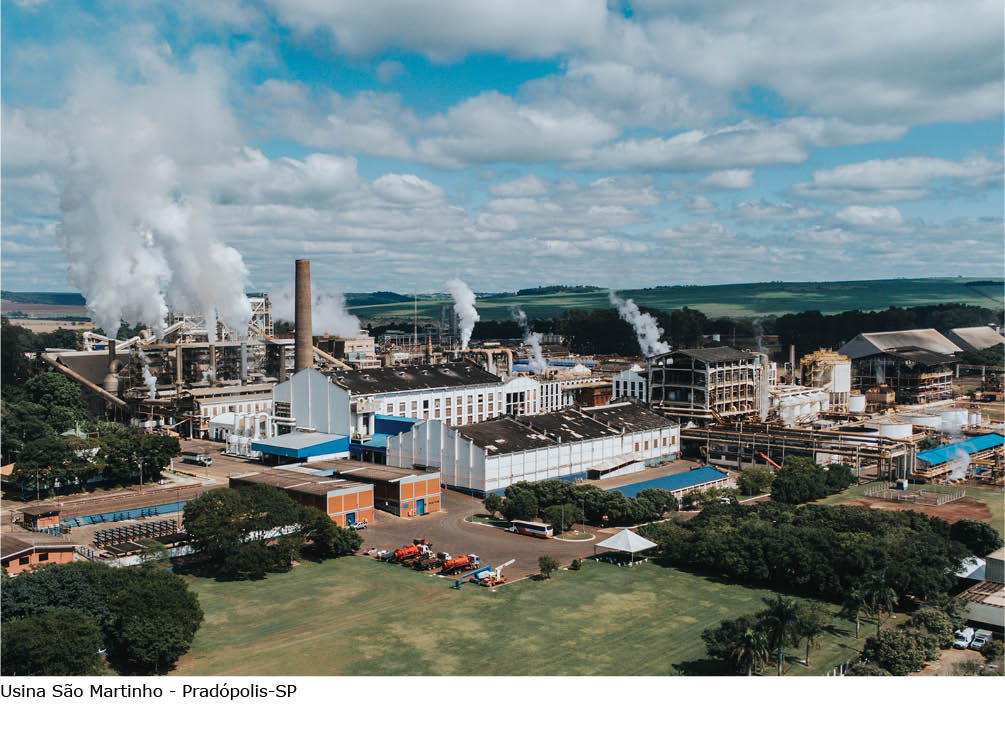