Os desafios enfrentados na área industrial do sistema sucroenergético sempre foram e continuam sendo os mais variados possíveis e precisam ser rapidamente identificados e continuadamente vencidos.
O mundo globalizado trouxe a concorrência e a competitividade, elevando a necessidade de as usinas serem autossuficientes e produzirem cada vez mais com maior rendimento e menores custos de produção. Dessa forma, surgiu a necessidade de uma gestão que visa a eliminação de perdas de processo e a operação de parâmetros industriais com excelência, garantindo não só a qualidade dos produtos finais acabados, mas, também, a qualidade do andamento do processo visando as Boas Práticas de fabricação.
Uma indústria só pode ser considerada eficiente quando se age diretamente nos gargalos que não lhe permitem atingir os indicadores e as metas estabelecidas.
Em uma usina sucroenergética, esses gargalos podem estar em todas as etapas do processo, desde a recepção da matéria-prima até a expedição do produto final. Como exemplo, um conjunto de moenda (Tandem) que não apresenta resultados de extração acima de 97% implica um percentual significativo perdido em ATR, podendo chegar a milhões de reais que deixaram de ser comercializados, desperdiçando açúcares efetivamente produzidos a partir da cultura da cana-de-açúcar com a utilização dos mais variados insumos e investimentos, que chegaram na usina e foram enviados para a caldeira juntamente com o bagaço.
Para uma melhor performance, deve-se buscar a melhor triangulação da moenda, sendo esse processo possível para todas as unidades, uma vez que o cenário não nos permite perder principalmente nas etapas iniciais do processo. A perda ideal em ATR é ≤ 3%.
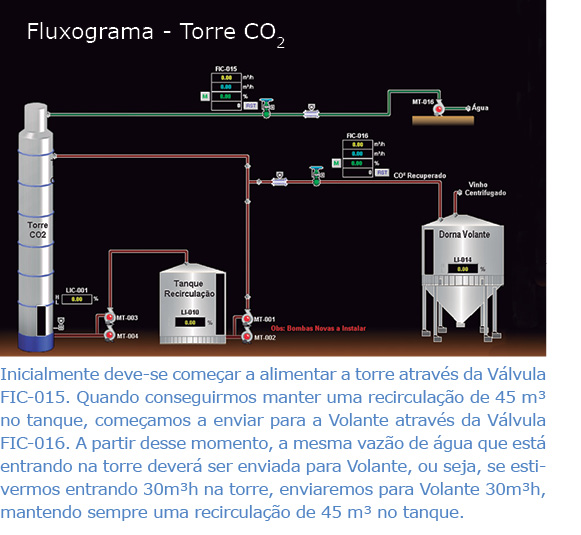
Sequenciando o processo de eficiência e transformação industrial, as perdas na torta de filtro podem ser resultantes de fatores intrínsecos ligados à operação do equipamento, como exemplo a falta de área filtrante; a velocidade do filtro; a falta de água de lavagem da torta e a temperatura da água de lavagem.
Também podem estar relacionadas simplesmente a um mau processo de realização da mistura do lodo, o que, se corrigido, pode apresentar números satisfatórios para um aumento da eficiência da planta. Essas variáveis são significativas para se obter um percentual de perda em ATR na faixa de 0,4%. A torta de filtro, é um outro ponto no qual é possível aumentar a produtividade simplesmente com o gerenciamento de variáveis controláveis do processo.
Podemos perder águas residuárias? Não, nunca! Essa perda é inadmissível, uma vez que essas águas são oriundas, muitas vezes, de uma cultura de descarte inadequado ou de um ineficiente gerenciamento de manutenção dos equipamentos e tubulações. Portanto, a manutenção industrial é uma importante ferramenta na busca por um processo que trabalhe sem desperdícios, com informações bem definidas gerando um feedback inteligente entre produção e manutenção. Os “setores de utilidades são prestadores de serviços na linha de produção”.
Outro ponto no qual é possível buscar o aumento da produtividade está relacionado ao processo de recuperação do etanol contido no CO2. Esse processo é realizado em torres nas quais acontece o processo de lavagem dos gases e a medição da eficiência a partir da água utilizada na lavagem; da quantidade de álcool produzido; da quantidade de álcool arrastado pelos gases e da quantidade de álcool extraído a partir da lavagem desses gases.
Porém, buscando maior eficiência desse processo, pode-se incrementar a ele um sistema denominado LCE (Lavar, Concentrar e Enviar). Nesse conceito é possível especificar o teor alcoólico desejado e trabalhar com o processo em sistema fechado, concentrando de tal forma que, somente após a concentração pré-estabelecida, será enviado para a volante, tendo seu funcionamento como um reprocesso trabalhando apenas com o desejado e, assim, otimizando a operação. Recuperação ≥ 1%. Conforme fluxograma em destaque.
Fermentar com alta eficiência! Eis uma questão muito delicada, uma vez que, a partir de uma alta eficiência fermentativa é possível alcançar valores de RTC (Recuperado Total Corrigido) em patamares desejáveis. Por outro lado, para que isso aconteça, é necessária a inibição da produção de subprodutos na fermentação e, para que isso ocorra, é necessário fermentar com boas temperaturas nas dornas, trabalhar com temperatura de mosto adequada, bons antissépticos e boa nutrição do meio, agindo de maneira correta na hora certa e resultando em um menor tempo de fermentação possível e um maior teor alcoólico. Consequentemente, um maior rendimento.
Não podemos falar de evolução industrial sem citar o balanço térmico, sendo este, fundamental para a sistemática de autossuficiência de uma usina. Ele torna possível a utilização de 360 kg de vapor por tonelada de cana em um conjunto formado por fábrica de açúcar, fábrica de etanol e fábrica de levedura e irrigação, retirando desse balanço somente a coogeração de energia.
Enfatizando que algumas usinas de bioeletricidade já conseguem trabalhar com valores abaixo desses, utilizando um projeto que conserva o alto valor de entalpia gerado na produção de vapor, diminuindo assim seu consumo específico. De toda água contida na cana-de-açúcar, 70% tem de servir ao processo em forma de água condensada.
Todos esses fatores de produção que foram citados somente são possíveis a partir de um nível elevado de comprometimento da equipe, juntamente com a automação dos processos vertentes, que é uma tendência comum a todas as plantas industriais. Do resultado de todas essas informações, se tem a anulação de forças que nos levariam a ser menos eficientes, transformando-as em forças de criatividade no grande processo de aumento de produtividade que elimina perdas e tem como consequência um alto índice de Recuperado Total Corrigido com baixos custos de produção. Menor risco, maior investimento; maior risco, menor investimento. Resumindo: Com um bom projeto e uma boa manutenção ocorre maior transformação.