O primeiro grande desafio para o sistema de extração foi o aumento da capacidade de processamento, utilizando de forma mais eficiente os ativos existentes nas instalações industriais. A introdução de alterações nos equipamentos existentes e os novos equipamentos nos sistemas de descarga, alimentação e preparo, com os revestimentos de solda tipo picote e chapisco nas moendas, progressivamente garantiram um aumento substancial na capacidade de moagem, para níveis sem precedentes e bem acima dos anteriormente obtidos em outros países para o mesmo porte de equipamento.
O segundo grande desafio para o sistema de extração nas usinas brasileiras foi o aumento da recuperação do açúcar da cana a ser enviado para o processo de fabricação. Esses desafios ocorreram a partir do início da década de 1970 e se desenvolveram ao longo dos anos, atingindo índices que nada deixavam a desejar quanto à capacidade, comparados a outros países produtores.
Outros desafios estavam relacionados com a redução dos custos de manutenção, do consumo de energia e da possibilidade de melhorar ainda mais os níveis de extração. Com esses propósitos, surgiram os primeiros difusores de cana na indústria brasileira no final da década de 1980.
Na evolução da tecnologia do processo de extração por moagem, a otimização energética ocorreu praticamente de forma simultânea com o desenvolvimento para aumento da capacidade; devido, principalmente, à utilização mais eficiente das moendas nos aspectos de alimentação e capacidade. Se, por um lado, algumas etapas do processo de extração utilizam equipamentos cujo consumo de energia é diretamente proporcional à taxa de processamento, como, no sistema de preparo da cana, no processo de moagem especificamente, o consumo de energia nem sempre é diretamente proporcional ao aumento da taxa de moagem?
Isso se deve ao fato de que o aumento da capacidade da moenda pode ser obtido pelo aumento da velocidade, e, nesse caso, o consumo de energia é diretamente proporcional ao aumento da taxa de moagem, ou apenas pelo aumento da sua capacidade volumétrica de alimentação com o aumento do diâmetro dos rolos. Nesse caso, o consumo de energia se mantém praticamente inalterado, diminuindo substancialmente seu consumo específico.
Por vezes, para aumentos maiores de capacidade, utiliza-se essas duas alternativas ao mesmo tempo e, ainda nesse caso, o aumento do consumo de energia fica aquém do aumento da taxa de moagem. Esse comportamento do consumo de energia é bem definido por E. Hugot (Handbook of Cane Sugar Engineering, 1986), comparando o aumento da capacidade da moenda pelo aumento das suas aberturas ou pelo aumento de sua velocidade.
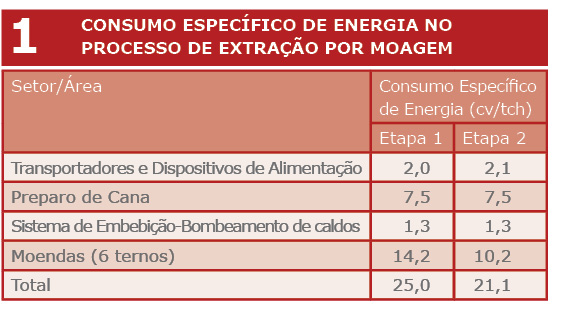
Da penúltima (etapa 1) para a última etapa (2) de evolução e aumento da capacidade da moenda, obtida pelo aumento de sua capacidade volumétrica e do diâmetro dos rolos, para uma instalação típica para ambos os casos, utilizando 1 picador de cana e 1 desfibrador do tipo leve (COP-5), podemos estimar o consumo específico de energia para essas duas etapas de aproximadamente 25 e 21 cv/tch, respectivamente. Essa diferença de 4 cv/tch é devida, praticamente, à diferença do consumo de energia específica no processo de moagem, conforme apresentado na Tabela 1.
Para as mesmas condições consideradas para o sistema de extração com moendas, desde a descarga da cana até a saída do bagaço no terno final de secagem, apenas alterando o desfibrador
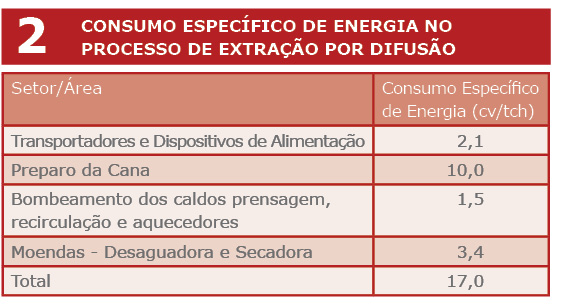
necessário para esse processo, o consumo específico de energia no processo de difusão é da ordem de pelo menos 17 cv/tch. Dependendo do tipo de desfibrador considerado, conforme apresentado na Tabela 2. Porém, é preciso atentar-se para o consumo de vapor em todo o processo de fabricação, pois o consumo de vapor de baixa pressão é maior nesse processo.
Apesar do menor consumo de energia, quando comparado com o processo de extração por moagem, o processo por difusão é muito sensível ao aumento da capacidade nominal de operação. Ele reduz significativamente o nível de extração devido à necessidade de adoção de maiores velocidades de operação, e também o tempo de retenção da cana no processo, conforme Peter Rein (Cane Sugar Engineering, 2007).
Para capacidades de moagem extremamente elevadas, na faixa de 25.000 a 30.000 TCD, deve-se considerar que é possível utilizar apenas 1 conjunto de moendas, enquanto no processo com difusores é necessário prever 2 linhas de operação, com forte impacto no investimento inicial e no custo de manutenção ao longo das safras.
Com o aumento da colheita mecânica de cana sem queimar e a eventual necessidade de maior quantidade de biomassa na indústria, a qualidade da cana sofreu alteração significativa em relação àquela processada anteriormente. Isso trouxe novos desafios para o processo de extração, uma vez que o aumento das impurezas resultou em queda da extração e da capacidade de processamento, com uma intensidade mais acentuada para os difusores. Para contornar esse problema, surgiram os sistemas de limpeza de cana a seco, um grande desafio para o setor, uma vez que ainda podemos considerá-la como uma tecnologia em desenvolvimento.
Ela possui diversas opções diferentes no mercado, com diferentes níveis de eficiência e com problemas específicos que ainda carecem de melhores soluções. Um agravante é que não existe uma metodologia padronizada para a avaliação de sua eficiência, e não se leva em conta que ela tem uma correlação muito forte com o teor de impurezas na cana sendo processada; ou seja, a eficiência de limpeza esperada para qualquer sistema deve sempre estar atrelada ao nível de impurezas na cana que será processada.
Recentemente, as camisas de alta drenagem ou camisas perfuradas, passaram a ser mais um recurso utilizado pela nossa indústria visando a melhoria da extração e da umidade do bagaço final, tendo como resultados adicionais a capacidade de moagem e redução do consumo de energia no processo de moagem. A melhoria da umidade pode ser observada claramente quando utilizadas no último terno do conjunto de moagem, com redução de 2 a 3 pontos com reflexo positivo na extração.
O aumento da capacidade pode ser observado quando utilizadas no 1º terno do conjunto de moagem, ou em qualquer terno intermediário do conjunto de moagem cujas dimensões sejam menores que as demais, além de propiciar uma operação mais estável quando utilizada em todos os ternos.
Segundo E. Hugot, o aumento da capacidade é o principal benefício da utilização das camisas perfuradas. O benefício com relação ao consumo de energia é devido ao aumento da quantidade de cana processada, na unidade de tempo, sem aumento do consumo de energia em relação à condição anterior.
Caso o objetivo não seja o aumento da capacidade horária, a mesma pode ser mantida em rotações menores, reduzindo o consumo de energia para a mesma quantidade de cana processada. O grande desafio é que há muito o que aprender e desenvolver com as camisas perfuradas abrangendo o seu projeto e seus efeitos na capacidade, extração e umidade, além das posições de instalação, pressão, entrada superior e/ou saída, que realmente se traduzam em benefícios pela sua utilização.
Concluindo, consideramos como desafios mais importantes atualmente para o processo de extração:
• Concluir o desenvolvimento de sistemas de limpeza a seco com maior eficiência;
• Simplificar o sistema de recepção, alimentação e preparo da cana;
• Aplicar as soldas nas moendas de forma mais eficiente através de sistemas robotizados; Utilizar de forma mais ampla e eficiente os benefícios das camisas perfuradas;
•Viabilizar a opção de utilização de difusores que, ao contrário das moendas, têm uma dependência negativa muito forte em relação à capacidade e à extração em função da qualidade da matéria prima.