A indústria mundial foi, é e sempre será pressionada por reduções de custos, melhoria de processos e elevação de qualidade. O avanço da tecnologia, o aumento da concorrência e a oferta maior do que a demanda de produtos são alguns de muitos fatores que levam os players do segmento sucroenergético a buscarem, cada vez mais, a diversificação, o conhecimento e a inovação para obter resultados vencedores.
Este artigo objetiva apresentar um programa desenvolvido para o gerenciamento de ativos das empresas em situações relacionadas a componentes mecânicos e visa gerar, através de ações de engenharia, oportunidades para obtenção de rentabilidades adicionais, proporcionando maior confiabilidade de máquinas, eficiência produtiva, maior conhecimento técnico e competitividade no segmento sucroenergético. A chave do sucesso é a interação da engenharia do fornecedor com os colaboradores do cliente, para identificar e compreender as questões e os problemas enfrentados no dia a dia, assim como o impacto financeiro ao negócio.
Métodos: Para dar início à gestão de ativos, deve ser efetuado o entendimento da organização e de seu contexto. A organização deve determinar as questões internas e externas pertinentes para as suas finalidades e que afetam sua habilidade em alcançar os resultados pretendidos na gestão de ativos. Os objetivos da gestão de ativos devem ser alinhados e consistentes com os objetivos organizacionais. Devem ser focados em adição de valor através de resultados técnicos e financeiros, com metodologia e processos definidos.
Proponho um programa dividido em quatro etapas: mapeamento, seleção, treinamentos e inspeção. Todas as atividades possuem um ciclo de cinco etapas, conforme gráfico do Ciclo de Adição de Valor –, que consistem em: análise da situação apresentada pelo cliente, proposta de solução adequada, implementação, monitoramento e a aprovação do projeto pelo cliente através de validação formal e a multiplicação para demais equipamentos e/ou áreas produtivas.
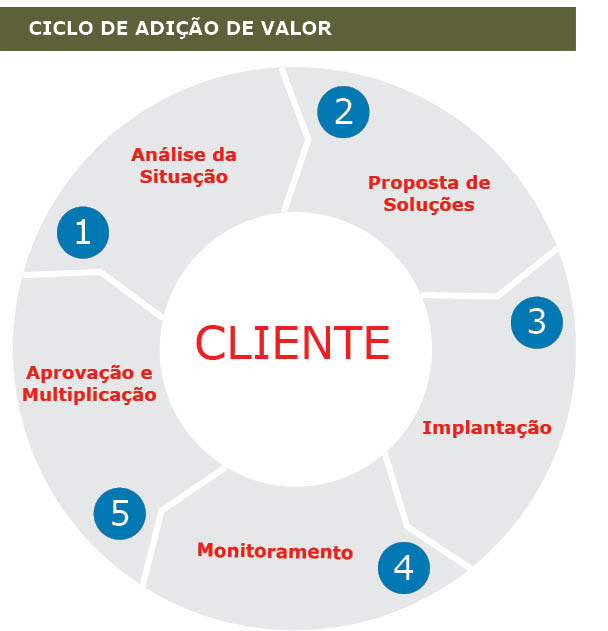
Mapeamento: Por muitas vezes, as empresas possuem problemas críticos que passam despercebidos durante anos, aumentando custos e reduzindo a lucratividade. Faz-se necessária a verificação dos processos, com destaque para oportunidades de melhorias. A primeira etapa proposta é o diagnóstico e a análise da planta. A manutenção de equipamentos ineficaz causa danos a muitas partes mecânicas. Ocorrendo a falha de um componente, vários distúrbios podem acontecer, inclusive problemas ambientais que afetam até mesmo a parada total da máquina, comprometendo todo o custo de produção.
Baseado na experiência do fabricante de um componente e nas aplicações do processo de fabricação, são identificados riscos e oportunidades de melhorias através da aplicação de questionário de risco, para identificação da análise situacional da empresa e definição do plano de ações, que deve contemplar questionamentos essenciais e ser efetuado junto ao cliente.
Deve ser definido um peso para cada um dos indicadores, e, em seguida, gerado um gráfico de tendências para identificação visual dos pontos a serem trabalhados, conforme demonstro no gráfico Tendências. Penso que o mapeamento de aplicações deve ser efetuado do início até o final do processo, identificando equipamentos, etapas críticas de produção e oportunidades de melhorias. Esse trabalho deve ser realizado pelo fabricante do componente, em conjunto com a manutenção e a produção do cliente. A partir dessa etapa, iniciam-se trabalhos de melhorias em equipamentos, focando a otimização da vida útil dos componentes.
A segunda atividade a ser desenvolvida é a auditoria do almoxarifado e da manutenção, que tem por objetivo identificar as condições de estocagem das peças, a verificação da qualidade do ambiente de instalação dos componentes, o ferramental e as práticas utilizadas no processo, visando operar conforme as melhores práticas de manutenção. É nessa etapa que serão identificados problemas com relação à estocagem de componentes e à necessidade de ferramentas de manutenção.
Seleção: O pilar de seleção começa com a revisão das aplicações. Essa atividade ocorre a partir da seleção de problemas críticos, atuando no projeto do equipamento de modo a atacar as causas raízes dos problemas, propondo e recomendando melhorias, sempre objetivando a redução de custos de manutenção através da análise de custo x benefícios. Nessa etapa, a equipe de engenharia do fornecedor deve realizar inspeções nas aplicações dos componentes dos principais equipamentos do processo (equipamentos críticos), com o intuito de detectar oportunidades de melhorias para aumentar a vida e performance dos componentes.
Em consequência, ganhos de performance em equipamentos críticos geram ganhos produtivos e financeiros elevados. Essa atividade é recomendada para aplicações em que o MTBF (tempo médio entre falhas) de componentes apresenta-se abaixo da normalidade, em equipamentos de criticidade “A”, que, ao falharem, potencializam perdas financeiras; em aplicações nas quais segurança, saúde e impacto ambiental podem ser afetados devido à falha dos componentes ou equipamentos; e em projetos (para aumento da capacidade produtiva do equipamento).
Outra atividade desse pilar é o trabalho de conversão de códigos de fabricantes de equipamentos originais e de outros fabricantes dos componentes. Essa atividade, muitas vezes, faz com que um produto possa ser adquirido com maior facilidade e rapidez, com custos reduzidos e qualidade equivalente ou superior, podendo representar uma grande redução de custos para o cliente. Por fim, a última atividade desse pilar abrange a análise e o diagnóstico da condição dos componentes em inspeções de temperatura, vibração e ruído.
Com a utilização dessas ferramentas, o cliente pode agir preventivamente em situações de possíveis falhas indesejadas. A atividade é recomendada para verificação das condições de equipamentos, aplicações em que falhas são comumente encontradas, aplicações com alto risco à segurança, à saúde e ao meio ambiente e a equipamentos críticos.
Treinamentos: Os treinamentos são um dos pilares com maior importância dentro do programa, que tem por princípio gerenciar os ativos do cliente final. Sendo os colaboradores da empresa preciosos ativos para a empresa, a forma como o conhecimento relativo ao produto é transmitido às equipes (engenharia, projetos, manutenção, operação e almoxarifado) faz com que a performance do componente e, por consequência, da máquina seja a maior e a melhor possível.
Através de conceitos e práticas, os cursos ministrados devem estar voltados para a realidade das empresas, com um único objetivo: aumentar a performance dos componentes aplicados. Penso que os módulos de treinamentos devem ser divididos em quatro níveis e abranger de conceitos generalistas a específicos. Como referência, podem-se definir níveis que variam de introdução ao produto, tecnologia do produto, práticas de manuseio e análise de falhas.
Inspeção: Muitos fatores afetam o desempenho dos componentes mecânicos. A análise de peças que falharam durante a aplicação e a identificação da causa raiz de falhas prematuras são de extrema importância. O fabricante do componente deve recomendar melhorias tanto para os equipamentos quanto para a correta seleção dos produtos. O acompanhamento de grandes paradas de manutenção, a inspeção de componentes em campo e a identificação da possibilidade de reutilização das peças através de técnicas de manutenção podem e devem ser amplamente explorados.
Dentro desse pilar, trabalha-se no acompanhamento e nas inspeções de campo; o departamento de engenharia do fabricante de produto deve dar ao cliente o suporte na instalação, remoção ou, ainda, na inspeção do produto em campo. Deve-se trabalhar também na análise do modo de falhas, orientando entender a causa raiz da falha de um produto através da análise do componente mecânico, de outros componentes da máquina e dos processos correlatos à aplicação.
É recomendada para aplicações de componentes estratégicos, que, ao falharem prematuramente em serviço, potencializam prejuízos ao cliente final; em situações de falhas repetidas, nas quais o componente é substituído com alta frequência; e em equipamentos de alta criticidade. Existem algumas situações em que a falha do componente mecânico necessita de uma análise com maior profundidade e criticidade para identificação da causa raiz.
São situações em que o suporte de engenharia de campo do fabricante não possui recursos suficientes para diagnosticar a falha. Nesses casos, o componente deve ser encaminhado para o fabricante realizar análises que possam indicar a causa da falha do produto e recomendar ao usuário como proceder para que a performance do componente mecânico seja adequada.
Conclusão: O gerenciamento de ativos de uma empresa requer o trabalho contínuo e de parceria entre o fabricante do produto e o cliente final. Para tanto, faz-se necessário o entendimento da organização, de seu contexto e das necessidades e das expectativas das partes interessadas, por meio de planejamento, assim como a definição de responsabilidades e papéis organizacionais. Além disso, o comprometimento de lideranças, a comunicação entre as partes e a busca por melhorias contínuas. Os benefícios de um programa como este são representativos e apresentam-se solucionando problemas, capacitando pessoas, aumentando eficiência produtiva, rentabilidade e competitividade do cliente e reduzindo tempo de paradas de máquinas.