É isso mesmo, controle avançado não funciona. Quantas vezes me deparei com essas afirmações dos nossos clientes quando começamos há mais de 10 anos? Não me refiro apenas a essa tecnologia, mas a muitas outras que, hoje, se enquadram no guarda-chuva do que chamamos de Indústria 4.0.
Hoje, olho para o passado e entendo que mercado e tecnologia têm que estar devidamente alinhados para se beneficiarem. É um casamento que precisa do amadurecimento das duas partes para que ocorra com sucesso. Hoje, o setor sucroenergético está mais preparado para absorver a tecnologia, e os fornecedores se adaptaram às necessidades específicas do mercado.
Até alguns anos atrás, o mercado estava acostumado a grandes ganhos de eficiência, provenientes de aumento de moagem e expansão fabril para equipamentos maiores e mais modernos, caldeiras de vapor a alta pressão, turbogeradores de múltiplos estágios, de alta eficiência, moendas eletrificadas, automação de processos manuais.
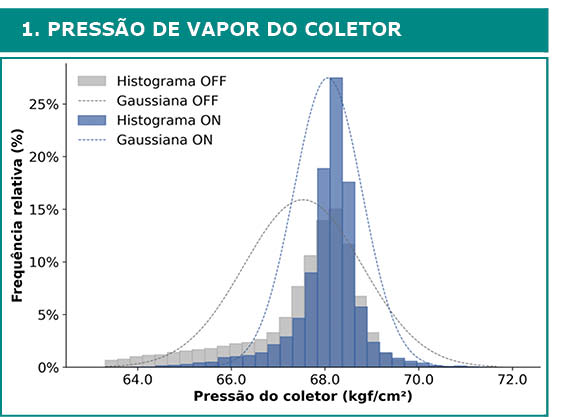
Os ganhos de eficiência eram facilmente visíveis, numa época de “mato alto”, que não existe mais. A direção se questiona: para que investir numa ferramenta complicada para ganhar 2% de eficiência, quando posso ter ganhos maiores, investindo para dar conta do aumento de moagem?
O modelo de negócio das soluções de Indústria 4.0 era baseado num relacionamento
make the sale and run, em que o fornecedor ofertava a licença dentro de um projeto e, após a conclusão, dava as costas, para que o cliente arcasse com a manutenção da ferramenta e suporte precário baseado em modelo
spot, lhe ficando a cargo todo o trabalho de validação e comprovação dos ganhos. O setor evoluiu e abraçou a era da Indústria 4.0.
Muita expectativa está sendo gerada, e levará um tempo para que ela case com os resultados trazidos por essas soluções mais inteligentes e baseadas em dados. A quantidade e a qualidade de dados fabris alcançaram novos patamares, com novos sistemas de automação e de instrumentação conectados em rede, historiadores de dados, sistemas de gestão de laboratório e sistemas de gestão agrícola, para citar alguns.
Muitas oportunidades de ganho de eficiência que estavam invisíveis para a gestão podem ser encontradas com uma boa análise de dados. Os fornecedores de soluções também se adaptaram e aperfeiçoaram o processo de aplicar com sucesso projetos de Indústria 4.0, adotando o modelo SaaS (
Software as a Service), mais alinhado com a busca do setor por projetos de
payback rápido e sem grandes investimentos envolvidos. Criaram-se métodos de avaliação estatística robustos que analisam o processo antes e depois da solução, com OPIs e KPIs técnicos.
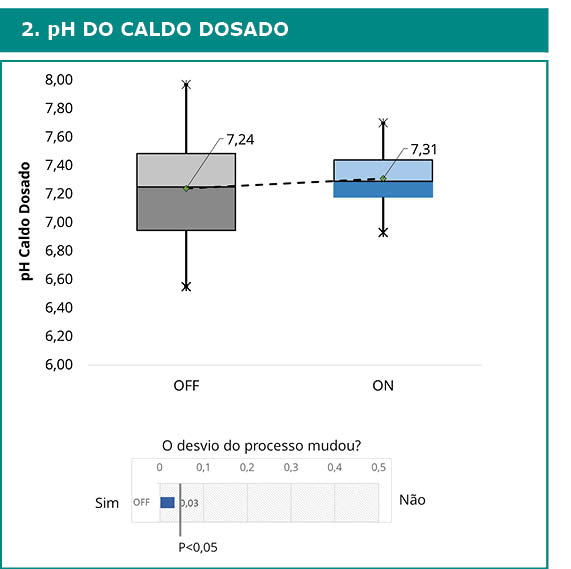
E, é claro, suporte continuado, no modelo de melhoria contínua, com acesso remoto à planta para análise de
performance dos sistemas. É um novo modelo de parceria que gera valor durante todo o ciclo de vida da solução e garante a perenidade dos resultados atingidos.
A Usina Conquista do Pontal (UCP), da Atvos, iniciou, em 2017, a implantação de sistemas de controle avançado em seus processos, com objetivo de atingir novos patamares de estabilidade de processo e
setpoints de operação mais econômicos. O primeiro foco de atuação foi na cogeração, com o objetivo de aumentar a eficiência na exportação e aproveitar o
boom do preço da energia na época.
Dentre os desafios desse tipo de processo, estava a necessidade de se prover um vapor de qualidade alta e constante para os turbogeradores, através da queima de um combustível de qualidade variável, como o bagaço de cana. Da mesma forma, o parque de turbogeradores deve atender às demandas de exportação de energia, sem comprometer a oferta de vapor para o processo.
Tanto a geração de vapor quanto a de energia elétrica são sistemas altamente acoplados; uma variação de processo em uma ponta gerará impacto significativo na outra parte e vice-versa. A solução escolhida pela Atvos para atender a esse desafio deveria ser capaz de observar múltiplas variáveis e tomar decisões em questões de segundos para atender à rápida dinâmica. A unidade já atendia a todos os requisitos para absorver o novo sistema de controle e, em menos de 8 semanas, já usufruía dos resultados.
Graças ao novo uso dos dados coletados pelos sistemas da UCP, foi possível estabilizar a pressão do vapor para as turbinas em 40%, promovendo um aumento de geração bruta de 2% e melhoria de consumo específico dos turbogeradores de 0,5%. Enquanto isso, a pressão de escape ficou 18% mais estável, reduzindo a ocorrência de alívios no processo em 86%.
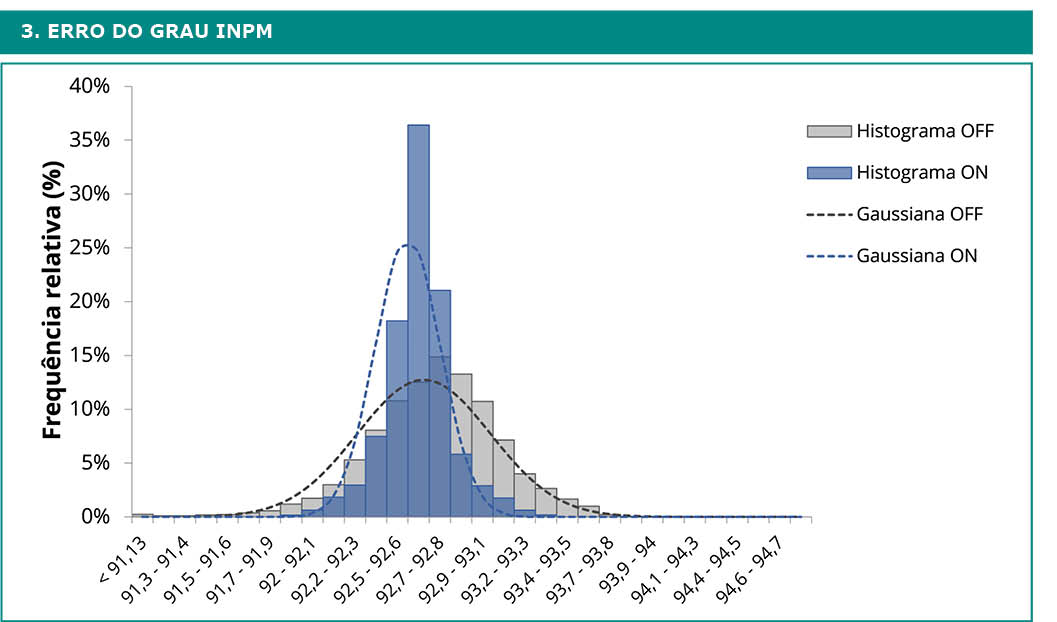
A partir desse
case de sucesso, a Atvos prosseguiu com a avaliação da solução em outras partes do processo. A estabilização da produção de vapor trouxe tantos benefícios indiretos que a unidade resolveu levar o mesmo conceito para a produção de açúcar.
Em 2018, a unidade prosseguiu com a expansão do sistema no tratamento de caldo; mais uma vez, ela estava preparada para adotar a ferramenta: sistemas de aquecimento, vazão de caldo e dosagem de cal automatizados e em rede, provendo o nível de dados adequado para o projeto.
Os desafios técnicos eram outros: não linearidade de um controle de pH, acoplamento da dinâmica dos múltiplos efeitos e a incrustação dos evaporadores que afetam a sua
performance. Mas a solução partia do mesmo princípio: dar nova utilização à informação fornecida pelo processo.
Nesse projeto, foi possível reduzir a variabilidade média do nível dos efeitos entre 10% e 33%, do pH do caldo dosado em 32% e reduzir a perda de pureza em até 19%. A unidade seguiu expandindo a aplicação do controle avançado na destilaria e na moenda, processos com dinâmicas e desafios completamente diferentes. A unidade se encontrava no nível de automação adequado para seguir com ambas as iniciativas.
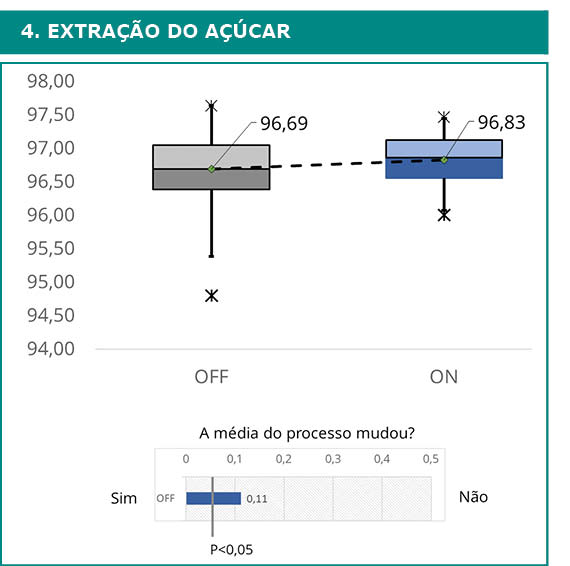
O projeto promoveu a redução de variabilidade do grau INPM do etanol em 40% e 50% em ambos os aparelhos, possibilitando o aumento de produtividade da destilaria, sem falar na redução das perdas alcoólicas. Na moenda, o sistema foi capaz de aumentar a extração em 0,08%, através do aumento da temperatura de embebição em 1ºC e da estabilidade da esteira do 1º terno em 26%, ao mesmo tempo, reduzindo o consumo de água bruta em 32%.
Todas essas avaliações foram realizadas com aplicação de métodos estatísticos robustos para evitar interferências externas, como definição de OPIs e KPIs técnicos, avaliação através de alternância com o sistema habilitado e desabilitado e a aplicação adequada de testes de significância para validar o nível de confiança dos resultados.
Além dos benefícios diretos, a parceria provê acompanhamento dobrado da calibração da instrumentação para correta medição dos benefícios, trabalho que é contínuo nesse modelo de parceria. Desde 2017, as soluções implementadas pela UCP são validadas com a Atvos para garantir a manutenção e a superação dos benefícios apurados na entrega do projeto.
A unidade pretende expandir a solução para a fábrica de açúcar e a fermentação, alcançando o conceito de “piloto automático” na operação e integrando a inteligência do controle avançado com o planejamento de produção.