Voltando ao passado para entender o presente, relembro que a evolução da indústria açucareira no Brasil, na área de extração de caldo, que permitiu o aumento da eficiência, escala e redução de custos, tem como marco o ano de 1973, quando a Copersucar contratou a consultoria do engenheiro sul-africano Denon Hullet, de cuja equipe tive a oportunidade de participar, implantaria técnicas desenvolvidas na Austrália e adaptadas na África do Sul.
A necessidade da procura de uma nova tecnologia de extração de caldo foi acelerada por dois programas governamentais: Prosucar e Proálcool. O objetivo era, inicialmente, o aumento da extração para diminuir perdas, porém também gerou um interessante resultado colateral, um progressivo aumento de capacidade de moagem. Antes de 1973, a média de perda de açúcar por tonelada de cana, medida pelo Laboratório Volante Copersucar, era de 15 kg açúcar/TC, enquanto, na África do Sul, nessa mesma época, era de 6 kg/TC. Hoje, temos valores abaixo de 4,5 kg/TC. Em 1973, uma moenda 78” moía 250 TCH (6.000 TCD); hoje, estamos acima dos 600 TCH (14.400 TCD).
Essa evolução fica clara quando analisamos o quadro do ocorrido com o passar dos anos. As mudanças que permitiram esse desenvolvimento são várias. No passado, o transporte da cana 100% inteira se fazia em caminhões com fueiro de madeira ou em feixes amarrados com correntes; hoje, se transporta a cana 100% picada, crua, em caçambas (90-100 m³) carregando até 35 toneladas. A descarga de cana era realizada por pontes rolantes que podiam alimentar diretamente a mesa ou formar um estoque no barracão para ser moído à noite, quando se utilizavam garras para alimentar a mesa.
Hoje em dia, se dá através de um ou mais hilos mecânicos ou hidráulicos, com capacidade de descarga de até 700 TCH por ponto. A recepção de cana deixou de lado as mesas alimentadoras de 12º e depois 45º e os longos esteirões metálicos, com corrente de 6” de passo e baixa qualidade, para dar lugar à moega receptora, com corrente de 8”, operando em baixa velocidade (5 m/min) – o que já permitiu um recorde de 7 safras sem trocar as correntes ou taliscas. Vale observar que a mudança de cana inteira para picada permitiu a retirada das mesas alimentadoras e esteirões metálicos.
Hoje, usamos transportadores de correia para transportar a cana da recepção ao equipamento de preparo. Em relação à limpeza da cana, a lavagem era feita na esteira e posterior nas mesas de 45º. Hoje, a limpeza da cana crua e picada é realizada por sopragem de ar a seco para a retirada das impurezas vegetais e minerais, o que foi mais um passo em direção a uma usina totalmente “seca”.
No preparo da cana, se utilizavam duas facas picadoras, que foram substituídas por uma faca picadora e um desfibrador (rotor com martelos pesados e placa desfibradora) instalado sobre a esteira metálica, evoluindo, atualmente, para um único rotor, com a passagem vertical da cana, o DVU, que prepara a cana tanto para moenda (open cell > 83%) como para o difusor (open cell > 90%). Esse sistema foi consequência da moagem de cana picada.
A alimentação do primeiro terno progrediu desde uma rampa aberta de descarga, ou esteira metálica forçada, juntamente com um rolo adensador para a calha vertical fechada, conhecida como Chute Donnelly. É preciso salientar o mérito dessa solução no aumento de moagem, pois possibilitou o aumento da densidade da cana alimentada nas moendas, e, com isso, houve um aumento da capacidade de moagem. Todos os avanços já relatados, somados à mudança do perfil da matéria-prima para cana picada, nos possibilitaram a seguinte solução em alimentação de cana: vale observar que um equipamento tem especial importância na mudança da alimentação e preparo de cana: é o DVU, que é um desfibrador vertical com apenas um rotor, que pode ser alimentado com transportador de borracha.
As usinas que processam exclusivamente cana picada e hoje usam o DVU tiveram um menor custo de implantação, pois eliminaram a mesa alimentadora e o esteirão metálico e têm um menor custo de operação, pois quase zeraram o custo com manutenção de correntes e diminuíram muito o consumo de energia. Para entregar open cell maior que 83% e 90%, o DVU consome, respectivamente, menos que 40 e 50 cv/TFH, um valor entre 20 e 30% menor quando comparado com outros sistemas tradicionais de preparo de cana.
Outra importante evolução desse sistema é a eliminação da perda de pol % cana que ocorre no esteirão de cana metálico, devido à necessidade de lavagem do mesmo. A evolução na moagem de cana pode ser claramente entendida com as seguintes fotos:
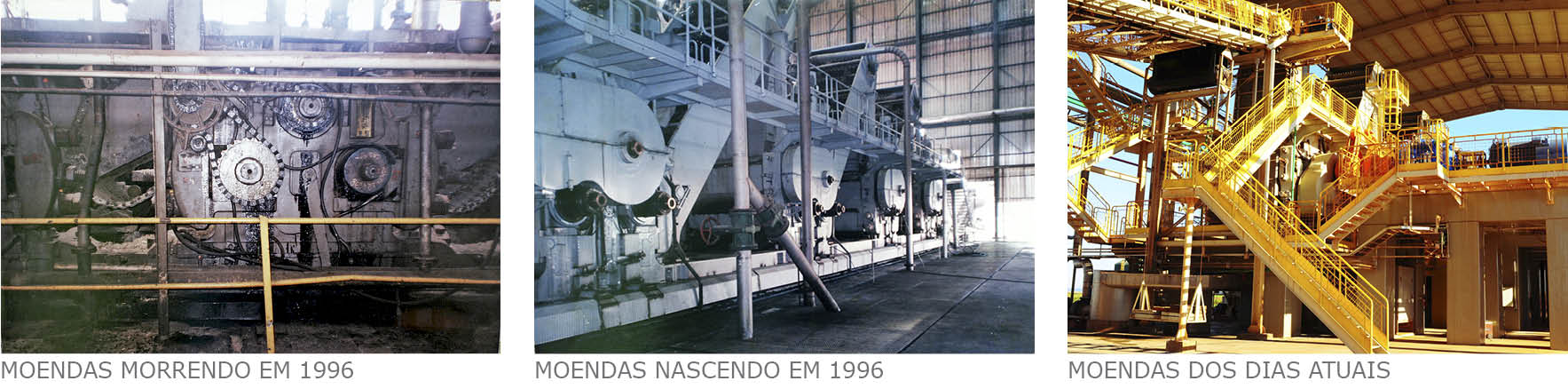
Voltando ao ano de 1973 para falar de moagem, lembramos que a tecnologia vinda da África do Sul, que, por sua vez, continha os estudos realizados na Austrália, preconizava:
-
novo critério para definir as aberturas entre rolos; • frisos de 1.½” e 2” de passo com ângulo de 35º; • instalação de um quarto rolo (rolo de pressão); • importante: aplicação de solda nos frisos (picote na crista e chapisco nas faces);
-
eliminação do uso de Chevrons e Messchaerts;
-
aplicação de embebição composta, colocando água quente (60 ºC) somente no último terno e retorno do caldo para as moendas anteriores sem coagem;
-
esteiras entre moendas com Donnellys em todos os ternos e a substituição do cush-cush de caldo misto por peneira rotativa.
Após muitos anos, é com certa satisfação que cito alguns dados obtidos nesta safra (2015, até julho):
E, em 2014, o recorde de moagem horária em uma mesma linha de moendas foi de 1480 TCH (1450 x 2500 + 1350 x 2300), o que permite atingir mais de 6 milhões de tonelada de cana por safra com apenas uma linha de moendas. Vale lembrar que a aplicação de uma engenharia mecânica mais apurada nos permitiu construir equipamentos mais precisos e resistentes, que nos proporcionaram um ganho de escala que apenas encontramos no nosso país, fato que teve grande influência na diminuição do “Capex” e “Opex” por tonelada de cana moída.
Falando de custo de manutenção por tonelada de cana da área de extração de caldo, a evolução tecnológica pela qual passamos e já descrevemos nos trouxe ganhos que podem ser claramente visualizados neste exemplo: Calculamos o custo de manutenção de duas unidades de um mesmo grupo, com práticas de manutenção idênticas:
-
Unidade A: Recepção por mesa, esteirão metálico, COP-8 e COP-5, moendas 66” e 54”.
-
Unidade B: Recepção por moega, transportadores de borracha, DVU, moendas 100” e 90”.
-
Resultado: A Unidade B tem um custo por tonelada moída que é praticamente a metade da unidade A. Nos tempos atuais, uma diferença dessa pode ter um impacto na saúde financeira das usinas.
Por fim, gostaria, de forma resumida, comentar o ganho energético e os malefícios que a moagem de cana crua podem trazer para a área de extração de caldo: além da já comentada possibilidade de simplificação das instalações, com redução de custos de implantação e operação, a cana crua pode nos proporcionar um grande ganho energético, pois os até 20% mais de biomassa que ela adiciona à usina pode ajudar muito no faturamento quando queimada em caldeira (energia) ou utilizada nos recém-implantados processos 2G.
Porém esse benefício não vem de graça, ele provoca dois sérios problemas, que são a perda de extração e da capacidade de moagem. Como média, podemos considerar que, a cada 1% de impurezas vegetais, a extração diminui em 0,15%, e a capacidade de moagem, em 1,2%. Porém esses problemas podem ser resolvidos pela aplicação dos, cada vez mais eficientes, sistemas de limpeza de cana a seco.
Concluindo: Após muita evolução, hoje, o grau de desenvolvimento tecnológico dos equipamentos da área de extração de caldo que temos disponíveis no Brasil torna nossas mais modernas usinas líderes mundiais quando tomamos como parâmetros:
-
Custo de implantação por tonelada de cana moída e açúcar extraído.
-
Custo de operação por tonelada de cana moída e açúcar extraído.